When you first come across embossing and debossing, it's natural to notice their striking similarities. Both techniques masterfully transform the surface of a material into a design that's not just a visual treat but also a delight to touch.
However, if you're wondering about what really sets them apart, you're not alone. Let's take a closer look, and we'll guide you through the distinctive qualities that make these two techniques unique in their own right.
Imagine embossing as a process that breathes life into a pattern, elevating it above the surface. It's akin to sculpting with paper, leather, or fabric, transforming these everyday materials into eye-catching, three-dimensional art.
Debossing, its equally artful counterpart, takes a different approach. This technique involves pressing the design into the material, resulting in an indented impression that captivates with its subtle charm.
Let's explore the differences between debossing and embossing, offering detailed insights into how these techniques can transform everything from books to letters and creative projects.
Embossing
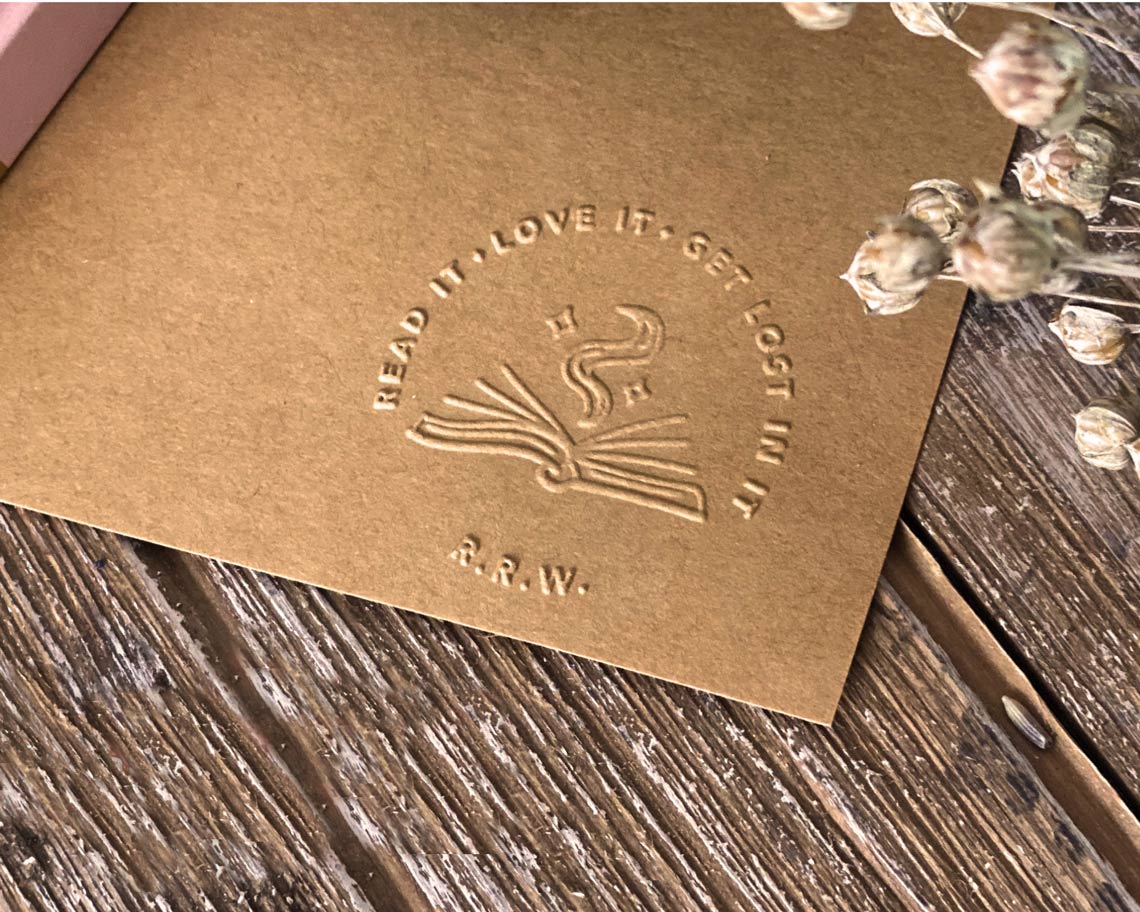
Embossing is an artistic technique used to create a raised, three-dimensional pattern on a malleable surface. It involves pressing an engraved design into the material, resulting in a textured image that stands out from the background. This technique transforms the tactile and visual experience of the material, lending it a sophisticated and elegant appearance.
How Embossing Works
The process of embossing starts with the creation of a metal die and counter-die, featuring the desired design. These dies are then used to apply high pressure to the material, such as paper or leather, sandwiching it between them. Depending on the technique, heat may be applied to enhance the embossing effect.
There are two primary types of embossing:
- Cold Embossing: This method does not use heat and is typically employed for materials sensitive to high temperatures.
- Hot Embossing: Involves applying heat, which softens the material, allowing for a more pronounced and detailed embossing.
Applications
Embossing is widely used in various industries due to its versatility and unique aesthetic appeal. Common applications include:
- Stationery: Embellishing business cards, wedding invitations, and award certificates.
- Publishing: Adding a tactile dimension to book covers and journal exteriors.
- Packaging and Branding: Enhancing product packaging and branding elements with a premium feel.
- Art and Decor: Creating textured artwork and decorative items.
Pros
- Aesthetic Appeal: Creates visually striking and tactilely engaging designs.
- No Ink Requirement: Can produce elegant designs without the need for inks or pigments.
- Detail and Precision: Capable of producing intricate and fine details in the design.
Cons
- Durability: Embossed areas can be prone to flattening or wear over time, especially in frequently handled items.
- Cost: Generally more expensive than standard printing methods due to the specialized equipment and process involved.
- Material Limitations: Best suited for malleable materials, limiting its application range.
Recent innovations in embossing have expanded its capabilities and applications. Digital variable embossing allows for more personalized and varied designs, while holographic embossing creates a multi-dimensional, shimmering effect.
Best practices in embossing emphasize the importance of choosing the right material and die design for each project, as well as considering finishing techniques such as adding color or protective layers to enhance and preserve the embossed design.
Debossing
Debossing is the inverse of embossing, where the design is recessed into the material instead of being raised. This technique involves pressing a design onto a material's surface, leaving an indented impression. Debossing creates a subtle yet impactful effect, providing a unique tactile experience and a visually distinct style.
How Debossing Works
The debossing process employs a metal die and counter-die, similar to embossing. The die, featuring the desired design, is pressed onto the surface of a material from above, pushing the design downwards to create a depression.
This can be achieved through:
- Cold Debossing: Applying pressure without heat, suitable for materials that might be heat sensitive.
- Hot Debossing: Incorporating heat to soften the material, allowing for a deeper and more defined indentation.
Applications
Debossing finds its use in various fields, lending a sophisticated and understated elegance to products. Key applications include:
- Branding: Used on leather goods, technology products, and corporate gifts for a refined branding effect.
- Signage and Plaques: Creating durable and permanent signage or commemorative plaques.
- Home Decor and Furniture: Adding depth and texture to items like photo frames, book covers, and furnishings.
Pros
- Durability: The impressions are long-lasting and resistant to wear, ideal for frequently used items.
- Accessibility: The tactile nature of debossing can aid in accessibility, especially for visually impaired users.
- Cost-Effectiveness: Often more affordable than embossing, especially for larger or more complex designs.
Cons
- Material Restrictions: Not suitable for delicate or highly flexible materials.
- Detail Limitations: Finer details and gradients can be challenging to achieve compared to embossing.
- Ink Dependency: To enhance visibility, debossed designs often require ink fills, adding to the process.
Debossing continues to evolve with technological advancements. Innovations like laser cutting and CNC machining have allowed for greater precision and creativity in debossed designs.
When implementing debossing, it is essential to consider the material's properties, the depth of the design, and potential finishing touches like inking or filling to ensure optimal visibility and effect.
Transform your paper crafts and stationery into works of art with our Custom Embosser!
Differences between Embossing vs Debossing
The artistic techniques of embossing and debossing are often used to add a unique tactile and visual dimension to various materials. While they share some similarities in their purpose and applications, they differ significantly in their execution, effects, and suitability for different materials.
Understanding these differences is crucial for choosing the right method for a specific design objective. Here, we delve into the key contrasts between embossing and debossing, exploring aspects like depth, durability, materials, aesthetics, cost, and inking requirements.
Aesthetics
Embossing and debossing differ in their tactile and visual impact. Embossing elevates a material's surface up to 1/16", creating a sophisticated, smooth raised effect. This is achieved by pressing the material into a die from below. Debossing, in contrast, indents the material up to 1/8" or more from above, resulting in a richly textured, recessed design.
These techniques not only alter the material's appearance but also its feel, with embossing being smooth to the touch and debossing offering a tactile depth. This depth and texture play a significant role in choosing between the two for their distinct aesthetic qualities.
Materials
Embossing is most effective on softer, more malleable materials like paper, leather, and vellum, which can easily be molded to create a raised design. Debossing, on the other hand, is better suited for harder, more rigid materials such as stainless steel, wood, and thick plastics, which can sustain the indented impressions effectively.
Durability
Debossed designs generally have a longer lifespan than embossed patterns. Embossed details can show wear and flattening within months, particularly on items that are handled frequently. Debossed impressions, however, are known for their lasting durability, often maintaining their form for decades, making them a preferable choice for items that require a long-lasting design.
Inking Differences
In embossing, the raised effect typically offers sufficient visibility and contrast, making inking less common. Debossing often relies on ink fills to enhance the visibility of the indented designs, especially on darker or textured materials. This need for inking in debossing can add an additional step to the process and influence the overall cost.
Cost
The costs associated with embossing and debossing can vary, with embossing generally being more expensive due to the specialized process and equipment required. Debossing might offer lower initial costs, but these can increase with the design's complexity and the type of materials used.
Which Should You Choose: Emboss vs Deboss?
When deciding between embossing and debossing, consider the unique characteristics and effects of each technique in relation to your project's needs. Choose embossing if you're aiming for a design that stands out with elegant, raised patterns, ideal for materials like paper and leather, and if you're focusing on aesthetic prominence in applications such as branding and decorative art.
On the other hand, opt for debossing for a more subtle, sophisticated effect, suitable for harder materials and applications where durability and a refined look are paramount.
Your choice should align with your project's material, desired aesthetic impact, durability needs, and budget considerations to ensure the final product perfectly embodies your creative vision.
Understanding Your Project's Needs
The decision between embossing vs debossing begins with a clear understanding of your project's objectives and the materials at your disposal. If your design goal is to create a visually striking and tactilely engaging piece, embossing might be the way to go. Its raised patterns are not just visually appealing but also add a unique texture to the surface.
On the other hand, if the project calls for a more understated yet sophisticated touch, debossing’s indented impressions provide an elegant solution. Additionally, the material you're working with plays a pivotal role. Softer materials like paper and thin cardstock are ideal for embossing, whereas tougher materials like leather and thick cardboards are better suited for debossing.
Practical Considerations
Durability and budget are two practical considerations that can greatly influence your choice. For designs that need to withstand frequent handling and use over time, debossing is often the more durable option. Its recessed designs are less prone to wear and damage compared to the raised surfaces of embossing.
When it comes to budget, embossing typically requires more specialized equipment and processing, which can translate to higher costs, especially for complex designs or large runs. Debossing, in general, can be a more cost-effective choice, particularly for projects with simpler designs or larger quantities.
Aesthetic and Functional Aspects
The visual impact of your design is another crucial factor. Embossing, with its raised design, is perfect for projects where you want the design to pop and grab attention, such as in branding and promotional materials. Debossing, with its subtle indentation, offers a refined look that can be more suitable for professional and elegant designs like high-end packaging or business stationery.
Functionally, consider how your audience will interact with the product. For instance, if you need your design to be legible and easily readable, the shadows cast by embossing or the depth provided by debossing can play a significant role.
Wrapping Up: Embossing vs. Debossing Decoded
In summary, embossing and debossing are more than just techniques; they are the gateway to adding depth, texture, and character to your projects. While embossing offers a raised, tactile experience that can elevate the aesthetics of your work, debossing provides a subtle, yet profound, depth that can lend a sophisticated feel. The choice between these two techniques hinges on a blend of artistic intent, material suitability, durability considerations, and budget constraints.
As you embark on your next design project, remember that the decision to use embossing or debossing should be informed by the unique aspects of your work and the message you wish to convey. Whether it's the bold statement of an embossed logo or the understated elegance of a debossed pattern, each method has the potential to transform your creative vision into a tangible reality. Embrace the power of these techniques to craft designs that not only capture the eye but also engage the touch.